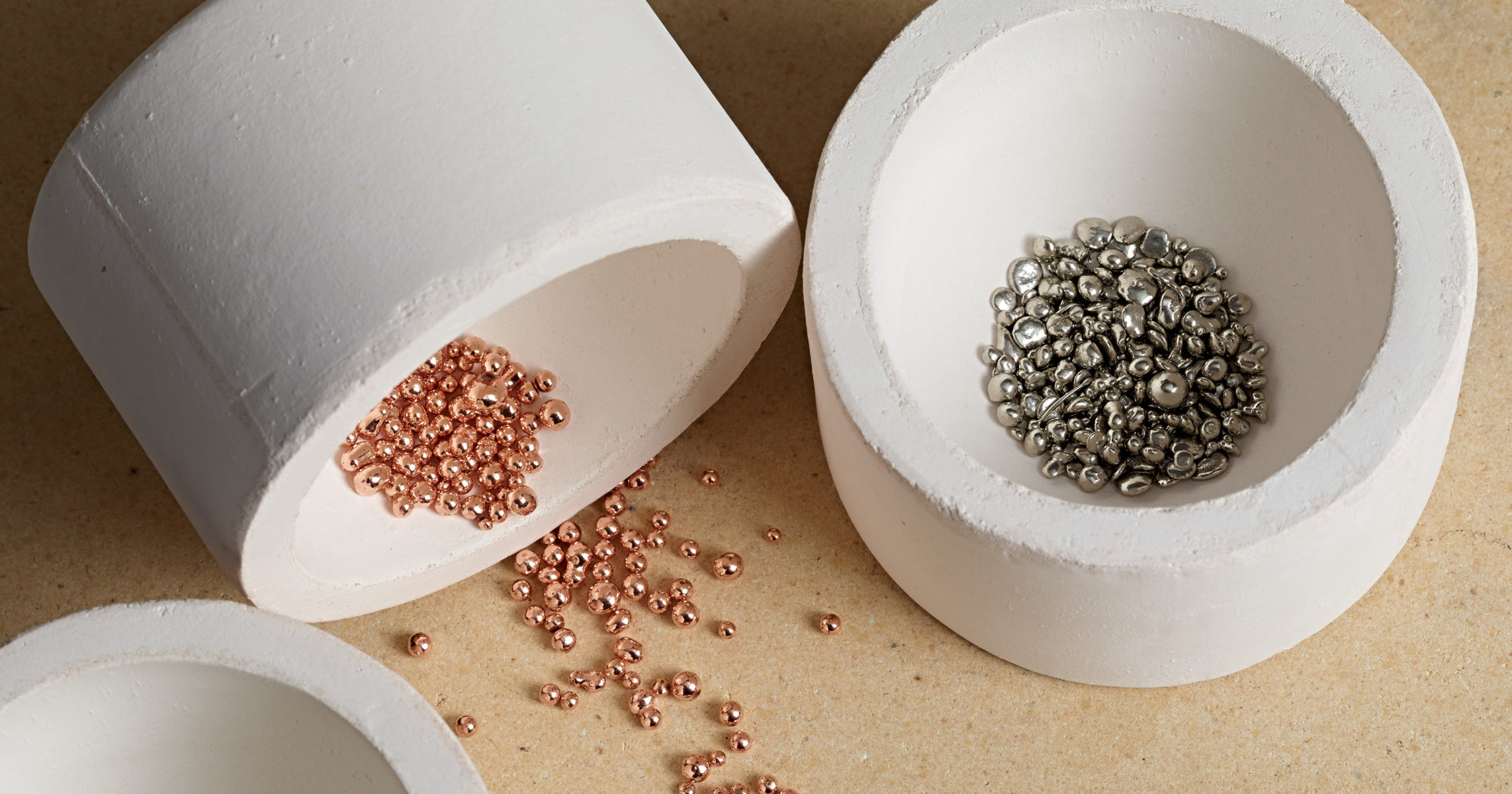
Metals Tech Experts Weigh In...
March is known for a few things – St. Patrick’s Day, March Madness, the Ides of March, and the list goes on. But for Stuller, March means it’s time for one of our most coveted events – the Bench Jeweler Workshop. And while COVID-19 hasn’t allowed us to host this event internally, we’ll be keeping traditional alive this month by featuring some of our more popular classes.
For this post, we went to our metals tech experts to pull tips that work well at the bench.
CHANGING THE KARAT OF GOLD
Up and down, you can adjust your on-hand karat gold following these instructions.
Raise the karat by adding pure (24k) fine gold.
Find your on-hand karat in the left column, and read across to your desired karat. The number at the intersection is your raising factor. Multiply this factor by the weight of your on-hand karat gold. The product gives you the weight of fine gold you must add to raise it to the desired karat.

Reducing the karat with alloy mix
Use the chart below in the same way you used the chart above. Start in the left column, selecting the karat you have on hand. Follow that line across to the karat you want. This number is your reducing factor. Multiply this factor by the weight of the on-hand karat gold, and you will get the amount of alloy mix you need to add.

GO WITH THE GRAIN–Don't cast with old gold
We strongly recommend casting with “fresh” grain. Old gold refers to scrap metal you’ve accumulated, taken in, or purchased from customers. Though this may appear to save you money, it can prove costly in time and quality in the long run. Most scrap includes various alloys that can interact, seriously affecting the metal’s color, mechanical properties, and casting properties.

Scrap may also include solder seams of antimony, bismuth, and even lead. These elements can cause complete casting failure. Cadmium and iridium, common to gold and silver, can affect the mechanical properties and soundness of casting.
Here are other issues about scrap.
• Rhodium plating can cause casting problems.
• Scrap karat can't always be determined, compromising the quality of a cast piece.
• You have no assurance that the scrap you purchase is high karat quality. Fatigued gold does not react as fresh metal does.
What’s the solution?
TIPS FOR RHODIUM PLATING
Rhodium plating is a regular part of your routine, but you’d be amazed at the number of calls we field on achieving perfect plating. Whether you’re plating a custom design or re-plating a well-worn ring, these tips will lead to success every time.
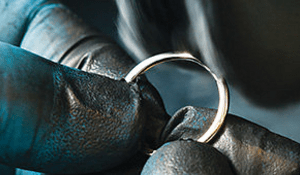
Above all: Keep your process simple by remembering, if it’s not clean, it won’t plate. Here’s what we mean by clean.
1. Polish the piece to a brilliant, high finish.
2. Clean thoroughly in an ultrasonic cleaner.
3. Rinse distilled water.
4. Steam clean.
5. For 30-60 seconds, electro clean at 100-120° F, using 2-6 volts in a stainless beaker with the positive lead attached to the beaker and the negative attached to the piece.
6. Rinse again in distilled water.
7. For 30-60 seconds, use an activator at room temperature with 0 volts.
8. Rinse yet again in distilled water.
When you have it squeaky clean, let the plating begin.
HEAT
For 15-25 seconds, heat the rhodium plating solution to 100° F, using 2-4 volts with the negative lead attached to the piece hung on a gold wire, and positive to platinum titanium anode. Note that the more time in the rhodium, the fewer volts; the less time, more volts.
RINSE
Rinse in distilled water.
STEAM
Steam dry and wipe with a soft cloth.
If it doesn’t go as smoothly as planned, you may see dark spots or a frosty finish. Try these troubleshooting tricks.
1. Be sure to use a gold hook to suspend the piece from an alligator clip for plating.
2. Never use copper in rhodium because it will contaminate your solution.
3. Keep your plating bath covered when it’s not in use.
Follow these steps every time, and you’ll enjoy consistent success.
10 AMP PLATING KIT

As always, if you need help with tools or equipment, contact Stuller’s Tools Tech Team. Give them a call at 1-800-877-7777, option 1.